Getting Started with Regenerative materials: A Beginner's Guide
We’re happy to hear you are thinking about starting your journey to develop using regenerative materials! If you're curious about sustainable manufacturing and the potential of creating products that are in harmony with the natural world, you're in the right place!
In this tutorial, we'll delve into the fundamentals of working with regenerative materials, providing you with a foundational understanding to kickstart your journey. Regenerative materials seamlessly integrate into nature's cycle, allowing their return without industrial intervention, sorting, or toxic repercussions for an ecosystems they rejoin. Fora more in-depth exploration of what constitutes regenerative materials and manufacturing see our article
here.
The first crucial step is identifying the specific functions your material needs to fulfill. Consider its desired strength properties, water resistance, flexibility (i.e. akin to leather), or hardness (like cement). Understanding these requirements sets the stage for selecting the right biomaterial and manufacturing process.
Choosing the appropriate material type holds greater significance in natural materials compared to technical ones, like plastic. When working with natural materials, adopt a mindset akin to Mother Nature's. Consider the specific requirements of your product, your customers' needs, its intended environment, and its role within the ecosystem where it will reside.
Reflect on how it interacts within that ecosystem and its ultimate impact on the environment. Mother Nature, with eons of evolution, has fine-tuned the needs of various products. However, we possess the advantage of swiftly testing and leveraging technology to iterate designs, adapting them efficiently to get to the product and process we envision.
There are various types of regenerative materials available, each with unique properties and applications. Cellulose-based materials come in both hard and soft variations, Calcium Carbonate materials, Fungi based materials, Algae based materials, Chitosan materials. Below an overview of the types of regenerative materials and potential sources
Cellulose-Lignin based
Cellulose, hemicellulose, and lignin are vital components found in plant cell walls, contributing to their structural integrity and durability. Among these, cellulose stands out as the most prevalent natural biopolymer on our planet.
From the familiar wooden products that form the basis of construction to finely powdered cellulose used in cosmetics as an exfoliant and as a key component in paper packaging, its uses span a wide spectrum. Moreover, cellulose's natural fibers are incorporated into textiles and materials to reinforce and strengthen them. One of the remarkable characteristics of cellulose is its high water absorbency relative to other biomaterials. This quality makes it valuable in applications where moisture resistance or absorption is needed, such as in certain paper products or textiles. When making products that need to be water tight be sure to use a natural protective barrier such as a wax or oil.
Common sources of Cellulose are wood chips, fruit pits (e.g olive pits) nut shells, paper waste and natural fibers such as Hemp. At Junai we use Olive pits in our cellulose based recipes to give products a wood type finish and light but strong properties.
Calcium Carbonate based
Calcium carbonate plays a pivotal role across diverse industries. Its strength and durability make it a cornerstone in construction materials like cement and concrete. Beyond construction, it finds application in pharmaceuticals, cosmetics, and food production due to its adaptable properties. In pharmaceuticals, calcium carbonate acts as an effective antacid and as a bulking agent.
Mined calcium carbonate has significant sustainability issues as it is often mined in vulnerable areas and needs significant heating before being used in construction. However, sicarded Oyster shells can also be a source of calcium carbonate, its production far less energy and resource intensive than the status quo.
Calcium carbonate, much like cellulose, is a crucial natural compound found abundantly in various sources, renowned for its versatility and wide-ranging applications. It is predominantly present in limestone, marble, chalk and as part of natural shells such as Oysters and Mussels. Calcium Carbonate can be present in (a mix of) three different phases, with different properties, calcite vaterite and aragonite.
At Junai we use Oyster shell as the main ingredient in our 3D printing paste
Chitosan
Chitosan is nature's second most prevalent biopolymer. Only Cellulose is more commonly used as a natural building block.
It is primarily derived from the exoskeletons of crustaceans like shrimp, crab, and lobster or from fungi.
Chitosan manifests in different forms, each with distinct characteristics and functionalities. Its presence as a biopolymer materializes in chitin, renowned for its versatile applications. It is used in diverse fields such as biomedicine, agriculture, wastewater treatment, and food packaging. In biomedicine, chitosan displays potential in wound healing due to its biocompatibility and antimicrobial properties. In agriculture, it serves as a natural biopesticide and plant growth enhancer, contributing to sustainable farming practices. Chitosan's unique properties also make it a favorable material in wastewater treatment, effectively removing pollutants and heavy metals.
While traditional extraction methods for chitosan may pose challenges in terms of sustainability and resource exploitation, exploring alternative sources such as fungal fermentation or using waste from seafood processing could pave the way for more environmentally friendly production methods. The current pricing of available chitosan in the market has limited the use cases in 3D printing applications for Junai
Fungi based materials
Mycelium is the vegetative part of a fungus, consisting of a network of thread-like structures called hyphae. It's essentially the root system of fungi and serves as the primary mode of nutrient absorption and distribution for the fungus. These fine, branching structures spread out and penetrate their surrounding environment, typically within soil, decaying organic matter, or other substrates where fungi thrive.
Mycelium serves as a biodegradable and renewable alternative to conventional materials like styrofoam, offering eco-friendly solutions for various product packaging needs. Additionally, mycelium-based materials show promise in construction, where they can be used as bio-composites or insulating materials, providing both structural support and environmental benefits.
Moreover, mycelium's unique properties allow it to be utilized in bioremediation, effectively breaking down pollutants and contaminants in soil and water.
We are currently using Mycelium as part of a new prototype packaging we are developing. It requires a clean environment, the right temperatures a good carrier to grow on and a mould to grow into. Moreover due to Mycelium being a live organism it can be challenging to work with the time constraints this creates.
Algae based materials
Algae-based biomaterials are derived from various types of algae, ranging from microalgae to macroalgae (seaweed). These biomaterials harness the natural properties of algae to create sustainable and versatile materials with a wide array of applications. Algae contain compounds such as polysaccharides, proteins, lipids, and pigments, which can be extracted and processed to form bioplastics, biofuels, fertilizers, pharmaceuticals, food supplements, and even textiles.
The production of algae-based biomaterials is generally considered environmentally friendly, as algae are highly renewable, grow rapidly, and can thrive in diverse environments, requiring minimal resources like land and freshwater. In recent years there has been more attention for regenerative ways of farming algae, to prevent issues similar to monoculture, pesticide based agriculture on land.
These materials also offer biodegradability and low environmental impact, making them increasingly sought-after alternatives. At Junai we use a seaweed derived binder, alginate.
When crafting a product using biomaterials, the beauty lies not only in individual sources but in the art of blending various materials. At our core, we believe in the power of fusion, exemplified by our blend of olive pit and oyster shell. Mixing different biomaterials isn't just an option; it's a canvas of possibilities waiting to be explored. By combining diverse elements, you can tailor the characteristics of your material to suit your specific application.
Step 3: Finding material sources
When determining the materials required for your project or production, it's pivotal to delve into the realm of sustainability and sourcing early on. This entails a comprehensive assessment of available materials, examining their eco-friendliness, and understanding the methods used for sourcing.
If you are starting your biomaterial journey from your own waste stream you will have 100% control over the origins and processing of the material. Otherwise there are various parties in the field that are able to provide supplies for your biomaterial product. At Junai we make our products locally and strive to make sure the entire supply chain is ethical and regenerative. You can find our materials
hereIf you are sourcing from other suppliers consider the following factors
1.
How close is it made to you? The more local, the more control you generally have on the process and limit logistics Co2.
2.
Is the supplier willing to share process information ? It is likely there are chemicals involved in processing, have a check to what extent energy and chemicals are needed for processing and if it fits your intended use and sustainability goals.
3.
What is the availability in small and larger volume? Often suppliers will have minimum order amounts, but are willing to share test products at smaller volumes. At Junai we provide materials starting from 250 gram and can scale that up. In general, suppliers will be able to get you better prices for higher volumes.
4.
What is the shape/fineness that the supplier will be delivering their product. Depending on your product, you might have specific requirements for the form the material needs to come in. At Junai for instance we exclusively work with powders at 200 mesh or smaller. This ensures the paste smoothly flows through our 3d printers.
Other resources to inspire you and find potential suppliers of your materias:
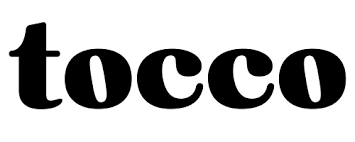
Tocco, a pioneering company in sustainable materials, boasts an expansive repository hosting over 5,000 regenerative materials that are refreshed daily. Their platform facilitates seamless connections between clients and global suppliers, enabling efficient sampling and collaborative product development with ease.
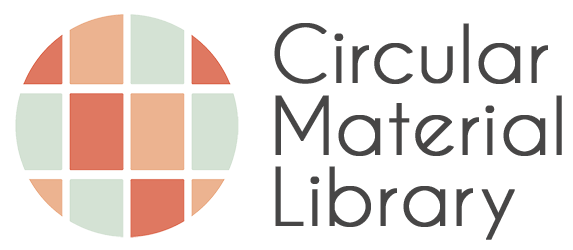
The Circular Material Library presents a comprehensive database featuring a diverse array of circular materials. Its distinct classification into 'TechCycle' and 'BioCycle' categories offers a valuable differentiation between technical and regenerative materials. We recommend to begin exploration with the biocycle section for a more sustainable selection.
Materiom
Materiom stands out as the foremost database, not merely a supplier overview but a rich repository of diverse recipes. Serving as an inspirational resource, it offers a wide array of formulations that serve as a springboard for creating personalized mixes.
Step 3: Finding the right manufacturing technique
From extrusion methods such as 3D printing to molding, sheet pressing, or the meticulous process of cutting and stitching, each technique demands specific materials and aligns differently with various product categories. Each method carries its own set of material prerequisites, tailored to optimize the manufacturing process and cater effectively to the unique attributes of the final product. Below a selection of first technologies we have tested with.
Extrusion
Extrusion is a manufacturing process that involves forcing a material, typically in a softened or molten state, through a shaped die to create a continuous profile or product. This is the process of all FDM and paste based 3D printing
Growing
Growing" refers to the utilization of molds to sculpt and fashion various live organisms, particularly employed in the formation of mycelium-based products. This technique harnesses the natural growth patterns of mycelium, guiding it to conform to specific shapes within molds, encouraging the mycelium to interlace and form strong, interconnected networks
Moulding/Pressing
Molding and pressing involves shaping materials by subjecting them to a mold or a cavity to acquire the desired form or directly pressing them into plates and bricks. It employs heat, pressure, or both to transform raw materials into specific shapes. With biomaterials often little to no heat is required, however as there is often a drying process cracks could appear due to shrinkage
Cutting
Cutting is the well known technioue of removing materials from a base shape to form the final product. With biomaterials this could involve simple sawing or you can use milling and/or lasercutting for more complex and intricate shapes
Begin by creating prototypes or small-scale versions using the selected regenerative materials and manufacturing methods. Test these prototypes against your defined material requirements, examining their performance, durability, and suitabilityfor your intended use. Biomaterial production isn't about getting it right the first time; it's about learning, refining working with your hand, enjoying yourself and living in harmony with nature. Keep it going through the many iterations and you'll be able to create something truly unique in a world filled with plastic products.
If you have any questions, need some personalised tips or just some encouragament please reach out to
jasper@junai.earth.
Authors